Calibração e Aferição de Instrumentos de Medição para Garantir Precisão e Confiabilidade
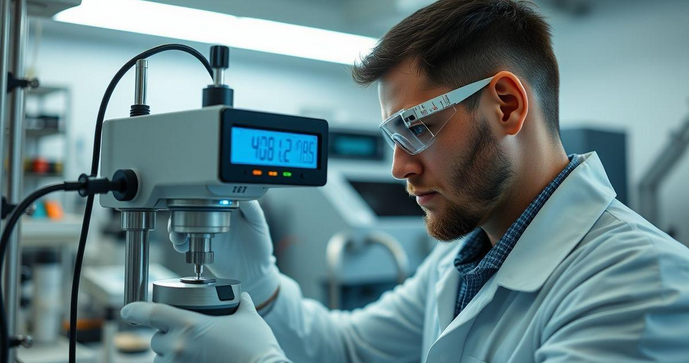
Por: Rafael - 24 de Abril de 2025
<p>A calibração e aferição de instrumentos de medição são processos fundamentais para garantir a precisão e a confiabilidade dos resultados em diversas aplicações industriais e laboratoriais. Esses procedimentos asseguram que os instrumentos estejam funcionando corretamente, evitando erros que podem comprometer a qualidade dos produtos e serviços. Neste artigo, abordaremos a importância da calibração e aferição, os métodos utilizados, a frequência recomendada para esses processos e os erros comuns que devem ser evitados.</p><h2>Importância da Calibração e Aferição na Indústria</h2><p>A calibração e aferição de instrumentos de medição são processos cruciais na indústria, pois garantem que os equipamentos utilizados para medir variáveis como pressão, temperatura, vazão e outros parâmetros estejam funcionando de maneira precisa e confiável. A precisão das medições é fundamental para a qualidade dos produtos, a segurança dos processos e a eficiência operacional. Neste contexto, entender a importância da calibração e aferição é essencial para qualquer profissional que atue em ambientes industriais.</p><p>Um dos principais motivos para a calibração e aferição é a necessidade de conformidade com normas e regulamentos. Muitas indústrias, especialmente aquelas que operam em setores regulados, como farmacêutico, alimentício e petroquímico, devem seguir padrões rigorosos estabelecidos por órgãos reguladores. Esses padrões frequentemente exigem que os instrumentos de medição sejam calibrados e aferidos regularmente para garantir que os resultados sejam válidos e aceitos. A não conformidade pode resultar em penalidades, multas e até mesmo a interrupção das operações.</p><p>Além da conformidade regulatória, a calibração e aferição são essenciais para a manutenção da qualidade do produto. Em processos de fabricação, pequenas variações nas medições podem levar a grandes discrepâncias na qualidade final do produto. Por exemplo, em uma linha de produção de alimentos, a medição incorreta da temperatura pode resultar em produtos não seguros para consumo. A calibração regular dos instrumentos de medição ajuda a garantir que as especificações do produto sejam atendidas, minimizando o risco de rejeição e retrabalho.</p><p>Outro aspecto importante é a eficiência operacional. Instrumentos de medição que não estão calibrados corretamente podem levar a decisões erradas, desperdício de materiais e aumento dos custos operacionais. Por exemplo, em um sistema de controle de processos, um medidor de vazão que não está calibrado pode resultar em uma dosagem incorreta de ingredientes, afetando a qualidade do produto e aumentando os custos. A calibração e aferição ajudam a otimizar os processos, garantindo que os instrumentos forneçam dados precisos e confiáveis, permitindo que as operações sejam realizadas de maneira mais eficiente.</p><p>A calibração e aferição também desempenham um papel fundamental na segurança dos trabalhadores e na proteção do meio ambiente. Em indústrias que lidam com substâncias perigosas, como produtos químicos e gases, a precisão das medições é vital para evitar acidentes. Instrumentos de medição que não estão calibrados podem levar a vazamentos, explosões e outras situações de risco. A calibração regular ajuda a garantir que os instrumentos estejam funcionando corretamente, minimizando o risco de acidentes e protegendo a saúde e segurança dos trabalhadores.</p><p>Além disso, a calibração e aferição contribuem para a confiabilidade dos dados coletados. Em muitas indústrias, os dados de medição são utilizados para análises e relatórios que influenciam decisões estratégicas. Se os dados não forem precisos, as decisões tomadas com base neles podem ser prejudiciais. A calibração e aferição garantem que os dados sejam confiáveis, permitindo que as empresas tomem decisões informadas e baseadas em evidências.</p><p>Um exemplo prático da importância da calibração e aferição pode ser observado no uso de medidores de vazão. O <a href="https://www.flowmetercalibra.com.br/medidor-vazao-agua-ultrassonico" data-inner-link="Medidor de vazão ultrassônico">Medidor de vazão ultrassônico</a> é amplamente utilizado em diversas aplicações industriais para medir a vazão de líquidos e gases. A precisão desse instrumento é crucial para garantir que os processos estejam operando dentro das especificações desejadas. A calibração regular do medidor de vazão ultrassônico assegura que ele forneça medições precisas, evitando desperdícios e garantindo a eficiência do sistema.</p><p>Por fim, a calibração e aferição não devem ser vistas apenas como uma obrigação regulatória, mas como uma prática essencial para a excelência operacional. Investir em calibração e aferição é investir na qualidade do produto, na segurança dos processos e na eficiência da operação. As empresas que adotam uma abordagem proativa em relação à calibração e aferição de seus instrumentos de medição estão mais bem posicionadas para enfrentar os desafios do mercado e garantir a satisfação do cliente.</p><p>Em resumo, a calibração e aferição de instrumentos de medição são fundamentais para a indústria, pois garantem a conformidade regulatória, a qualidade do produto, a eficiência operacional e a segurança. A implementação de práticas regulares de calibração e aferição é um passo essencial para qualquer empresa que busca manter altos padrões de qualidade e segurança em suas operações.</p><h2>Métodos Comuns de Calibração e Aferição</h2><p>A calibração e aferição de instrumentos de medição são processos essenciais para garantir a precisão e a confiabilidade dos dados coletados em diversas aplicações industriais. Existem vários métodos utilizados para realizar esses processos, cada um com suas características e adequações específicas. Neste artigo, abordaremos os métodos mais comuns de calibração e aferição, destacando suas vantagens e aplicações.</p><p>Um dos métodos mais tradicionais de calibração é a calibração por comparação. Neste método, o instrumento a ser calibrado é comparado a um padrão de referência que possui uma precisão conhecida. O padrão de referência pode ser um instrumento de medição de alta precisão, que foi calibrado anteriormente e é rastreável a padrões nacionais ou internacionais. Durante o processo, as medições do instrumento em teste são comparadas com as do padrão, e as discrepâncias são registradas. Esse método é amplamente utilizado em laboratórios e indústrias, pois permite identificar rapidamente desvios e ajustar o instrumento conforme necessário.</p><p>Outro método comum é a calibração por ajuste. Neste caso, o instrumento é ajustado diretamente para que suas medições correspondam às do padrão de referência. Esse método é frequentemente utilizado em instrumentos que possuem um mecanismo de ajuste interno, como termômetros e manômetros. A calibração por ajuste é eficaz, pois não apenas identifica desvios, mas também corrige o instrumento, garantindo que ele forneça medições precisas. No entanto, é importante que esse ajuste seja realizado por profissionais qualificados, para evitar danos ao instrumento.</p><p>A calibração em campo é um método que se tornou cada vez mais popular, especialmente em indústrias que utilizam instrumentos de medição em locais remotos ou de difícil acesso. Nesse método, os instrumentos são calibrados no local de uso, utilizando padrões de referência portáteis. A calibração em campo é vantajosa, pois minimiza o tempo de inatividade dos equipamentos e permite que as medições sejam verificadas em condições reais de operação. No entanto, é fundamental que os padrões utilizados sejam devidamente calibrados e rastreáveis.</p><p>Além dos métodos mencionados, a calibração por simulação é outra abordagem utilizada, especialmente em instrumentos eletrônicos. Nesse método, um sinal de entrada conhecido é aplicado ao instrumento, e a saída é medida. A comparação entre a saída do instrumento e o sinal de entrada permite verificar a precisão do equipamento. A calibração por simulação é particularmente útil para instrumentos que não podem ser ajustados fisicamente, como sensores de pressão e temperatura. Esse método é amplamente utilizado em laboratórios de calibração e em ambientes industriais onde a precisão é crítica.</p><p>A aferição, por sua vez, é um processo que envolve a verificação da conformidade de um instrumento de medição com padrões estabelecidos. A aferição pode ser realizada de forma semelhante à calibração, mas geralmente não envolve ajustes no instrumento. Em vez disso, a aferição fornece um relatório que indica se o instrumento está dentro das especificações aceitáveis. Esse processo é essencial para garantir que os instrumentos atendam aos requisitos regulatórios e de qualidade. Muitas <a href="https://www.flowmetercalibra.com.br/empresas-calibracao-equipamentos" data-inner-link="Empresas de calibração de equipamentos">empresas de calibração de equipamentos</a> oferecem serviços de aferição, permitindo que as indústrias mantenham seus instrumentos em conformidade com as normas aplicáveis.</p><p>Outro método importante é a calibração por transferência. Esse método é utilizado quando não é possível calibrar um instrumento diretamente em relação a um padrão de referência. Em vez disso, um instrumento de medição calibrado é utilizado para medir a saída de outro instrumento. A calibração por transferência é comum em situações em que os instrumentos são grandes ou pesados demais para serem transportados para um laboratório de calibração. Esse método é eficaz, mas requer que o instrumento de transferência seja calibrado e rastreável.</p><p>Além dos métodos tradicionais, a tecnologia moderna trouxe novas abordagens para a calibração e aferição. A calibração automatizada, por exemplo, utiliza sistemas de software e hardware para realizar calibrações de forma mais rápida e precisa. Esses sistemas podem ser programados para realizar calibrações em intervalos regulares, garantindo que os instrumentos estejam sempre dentro das especificações. A calibração automatizada é especialmente útil em ambientes industriais onde a eficiência e a precisão são essenciais.</p><p>Por fim, é importante ressaltar que a escolha do método de calibração e aferição deve levar em consideração diversos fatores, como o tipo de instrumento, a precisão necessária, o ambiente de operação e os requisitos regulatórios. Cada método possui suas vantagens e desvantagens, e a seleção adequada pode impactar significativamente a qualidade das medições e a eficiência dos processos industriais.</p><p>Em resumo, os métodos de calibração e aferição são fundamentais para garantir a precisão e a confiabilidade dos instrumentos de medição. A calibração por comparação, ajuste, em campo, simulação e transferência, assim como a aferição, são algumas das abordagens utilizadas na indústria. A escolha do método adequado é essencial para manter a qualidade e a conformidade dos processos, assegurando que as medições atendam aos padrões exigidos.</p><h2>Frequência Recomendada para Calibração de Instrumentos</h2><p>A calibração de instrumentos de medição é um processo vital para garantir a precisão e a confiabilidade dos dados coletados em diversas aplicações industriais. No entanto, a eficácia da calibração não depende apenas da qualidade do processo em si, mas também da frequência com que é realizada. A determinação da frequência recomendada para calibração é um aspecto crucial que pode impactar diretamente a qualidade do produto, a segurança dos processos e a eficiência operacional. Neste artigo, discutiremos os fatores que influenciam a frequência de calibração e as recomendações gerais para diferentes tipos de instrumentos.</p><p>Um dos principais fatores a serem considerados ao determinar a frequência de calibração é o tipo de instrumento utilizado. Instrumentos que operam em ambientes mais rigorosos ou que estão sujeitos a condições extremas, como temperatura, pressão e umidade, geralmente requerem calibrações mais frequentes. Por exemplo, um <a href="https://www.flowmetercalibra.com.br/venda-medidores-vazao" data-inner-link="Medidor de vazão">medidor de vazão</a> que é utilizado em um ambiente industrial com variações constantes de temperatura e pressão pode sofrer desgastes mais rapidamente, exigindo calibrações regulares para garantir medições precisas. Em contrapartida, instrumentos que operam em condições mais estáveis podem ter intervalos de calibração mais longos.</p><p>Outro fator importante é a frequência de uso do instrumento. Instrumentos que são utilizados com alta frequência, como aqueles em linhas de produção, estão mais propensos a apresentar desvios em suas medições. Portanto, é recomendável que esses instrumentos sejam calibrados com mais regularidade. Por outro lado, instrumentos que são utilizados esporadicamente podem ter intervalos de calibração mais longos, desde que sejam mantidos em boas condições e armazenados adequadamente quando não estiverem em uso.</p><p>A natureza do processo em que o instrumento está inserido também desempenha um papel significativo na determinação da frequência de calibração. Em indústrias onde a precisão é crítica, como na farmacêutica ou na alimentícia, a calibração deve ser realizada com mais frequência para garantir que os produtos atendam aos padrões de qualidade e segurança. Em contrapartida, em processos onde a margem de erro é maior, a frequência de calibração pode ser reduzida. É fundamental que as empresas avaliem os riscos associados a medições imprecisas e ajustem a frequência de calibração de acordo.</p><p>Além disso, as recomendações dos fabricantes dos instrumentos devem ser levadas em consideração. Muitos fabricantes fornecem diretrizes específicas sobre a frequência de calibração para seus produtos, com base em testes e experiências anteriores. Essas recomendações são valiosas e devem ser seguidas para garantir que os instrumentos funcionem conforme esperado. Ignorar as orientações do fabricante pode resultar em medições imprecisas e comprometer a qualidade do produto final.</p><p>As normas e regulamentos aplicáveis à indústria também influenciam a frequência de calibração. Muitas indústrias são obrigadas a seguir normas específicas que estabelecem requisitos de calibração e aferição. Por exemplo, a ISO 9001, uma norma internacional de gestão da qualidade, recomenda que as organizações estabeleçam procedimentos para a calibração de instrumentos de medição, incluindo a definição de intervalos de calibração. As empresas devem estar cientes das normas que se aplicam ao seu setor e garantir que suas práticas de calibração estejam em conformidade.</p><p>Um aspecto importante a ser considerado é a análise de histórico de desempenho do instrumento. Acompanhar o desempenho de um instrumento ao longo do tempo pode fornecer informações valiosas sobre a necessidade de calibrações mais frequentes. Se um instrumento apresentar desvios frequentes ou inconsistências nas medições, pode ser um sinal de que a frequência de calibração deve ser aumentada. Por outro lado, se um instrumento demonstrar um desempenho consistente e confiável ao longo do tempo, a frequência de calibração pode ser ajustada para um intervalo mais longo.</p><p>Por fim, a implementação de um programa de manutenção preventiva pode ajudar a otimizar a frequência de calibração. A manutenção regular dos instrumentos, incluindo limpeza e verificação de componentes, pode contribuir para a estabilidade das medições e reduzir a necessidade de calibrações frequentes. Um programa de manutenção bem estruturado pode ajudar a identificar problemas antes que eles afetem a precisão do instrumento, permitindo que as calibrações sejam realizadas de forma mais eficiente.</p><p>Em resumo, a frequência recomendada para calibração de instrumentos de medição é influenciada por diversos fatores, incluindo o tipo de instrumento, a frequência de uso, a natureza do processo, as recomendações do fabricante, as normas aplicáveis e o histórico de desempenho. As empresas devem avaliar cuidadosamente esses fatores e estabelecer um cronograma de calibração que atenda às suas necessidades específicas. A calibração regular é essencial para garantir a precisão e a confiabilidade das medições, contribuindo para a qualidade do produto e a eficiência operacional.</p><h2>Erros Comuns na Calibração e Como Evitá-los</h2><p>A calibração de instrumentos de medição é um processo crítico que garante a precisão e a confiabilidade das medições em diversas aplicações industriais. No entanto, erros podem ocorrer durante esse processo, comprometendo a qualidade dos resultados. Identificar e evitar esses erros é fundamental para garantir que os instrumentos funcionem corretamente e que os dados coletados sejam válidos. Neste artigo, discutiremos os erros comuns na calibração e como evitá-los.</p><p>Um dos erros mais frequentes na calibração é a falta de um padrão de referência adequado. A calibração deve ser realizada em comparação com um padrão que tenha uma precisão conhecida e que seja rastreável a padrões nacionais ou internacionais. Utilizar um padrão inadequado pode resultar em medições imprecisas e comprometer a confiabilidade dos dados. Para evitar esse erro, é essencial que as empresas utilizem padrões de referência que sejam regularmente calibrados e que atendam às especificações necessárias. Além disso, é importante que os profissionais responsáveis pela calibração estejam cientes da importância de utilizar padrões adequados.</p><p>Outro erro comum é a calibração em condições inadequadas. A temperatura, umidade e pressão do ambiente podem afetar significativamente os resultados da calibração. Realizar a calibração em um ambiente que não atenda às condições recomendadas pelo fabricante pode levar a desvios nas medições. Para evitar esse problema, as empresas devem garantir que a calibração seja realizada em um ambiente controlado, onde as condições sejam monitoradas e mantidas dentro dos limites especificados. Isso inclui a utilização de equipamentos de climatização e a realização de calibrações em locais apropriados.</p><p>A falta de treinamento adequado dos profissionais que realizam a calibração é outro fator que pode levar a erros. A calibração é um processo técnico que requer conhecimento e habilidades específicas. Profissionais não treinados podem cometer erros ao realizar medições, ajustes ou interpretações dos resultados. Para evitar esse problema, as empresas devem investir em treinamento contínuo para suas equipes, garantindo que todos os envolvidos no processo de calibração estejam atualizados sobre as melhores práticas e procedimentos. Além disso, a documentação de procedimentos e a realização de auditorias internas podem ajudar a identificar áreas que necessitam de melhorias.</p><p>Um erro comum que pode ocorrer durante a calibração é a falta de manutenção dos instrumentos de medição. Instrumentos que não são mantidos adequadamente podem apresentar desgastes e falhas que afetam a precisão das medições. A manutenção regular, incluindo limpeza, verificação de componentes e ajustes, é essencial para garantir que os instrumentos estejam em boas condições de funcionamento. As empresas devem implementar um programa de manutenção preventiva que inclua a verificação regular dos instrumentos e a realização de calibrações conforme necessário. Isso não apenas ajuda a evitar erros, mas também prolonga a vida útil dos equipamentos.</p><p>A calibração inadequada dos instrumentos também pode ser um problema. Isso pode ocorrer quando os ajustes são feitos de forma incorreta ou quando as medições não são registradas corretamente. Para evitar esse erro, é importante que os profissionais sigam rigorosamente os procedimentos de calibração estabelecidos e que todos os resultados sejam documentados de forma precisa. A utilização de checklists durante o processo de calibração pode ajudar a garantir que todas as etapas sejam seguidas e que os resultados sejam registrados corretamente.</p><p>Outro erro que pode ocorrer é a falta de rastreabilidade dos resultados de calibração. A rastreabilidade é fundamental para garantir que os resultados sejam válidos e que possam ser verificados. A falta de documentação adequada pode levar a questionamentos sobre a precisão das medições e à não conformidade com normas e regulamentos. Para evitar esse problema, as empresas devem manter registros detalhados de todas as calibrações realizadas, incluindo informações sobre os padrões utilizados, as condições de calibração e os resultados obtidos. Isso não apenas ajuda a garantir a conformidade, mas também facilita a identificação de problemas e a implementação de melhorias.</p><p>Além disso, a escolha inadequada da frequência de calibração pode levar a erros. Calibrar instrumentos com muita frequência pode resultar em custos desnecessários, enquanto calibrá-los com pouca frequência pode comprometer a precisão das medições. As empresas devem avaliar cuidadosamente a frequência de calibração com base em fatores como o tipo de instrumento, a frequência de uso e as condições de operação. Consultar uma <a href="https://www.flowmetercalibra.com.br/empresas-calibracao-instrumentos-medicao-sp" data-inner-link="Empresa de calibração de instrumentos de medição">empresa de calibração de instrumentos de medição</a> pode ajudar a determinar a frequência adequada e a garantir que os instrumentos estejam sempre em conformidade.</p><p>Por fim, a falta de comunicação entre as equipes envolvidas no processo de calibração pode levar a erros. É fundamental que todos os profissionais envolvidos estejam cientes dos procedimentos, das expectativas e dos resultados esperados. A comunicação eficaz pode ajudar a evitar mal-entendidos e garantir que todos trabalhem em conjunto para alcançar os objetivos de calibração. Reuniões regulares e a utilização de ferramentas de comunicação podem facilitar a troca de informações e a colaboração entre as equipes.</p><p>Em resumo, os erros comuns na calibração de instrumentos de medição podem comprometer a precisão e a confiabilidade dos dados coletados. A falta de padrões adequados, condições inadequadas, treinamento insuficiente, falta de manutenção, calibração inadequada, falta de rastreabilidade, escolha inadequada da frequência de calibração e falta de comunicação são alguns dos principais erros que podem ocorrer. Ao identificar e evitar esses erros, as empresas podem garantir que seus instrumentos de medição funcionem corretamente e que os dados coletados sejam válidos e confiáveis.</p><p>Em conclusão, a calibração e aferição de instrumentos de medição são essenciais para a manutenção da qualidade e segurança em ambientes industriais e laboratoriais. Através da compreensão da importância desses processos, da aplicação de métodos adequados, da definição de frequências apropriadas e da identificação de erros comuns, as empresas podem garantir que seus instrumentos operem com precisão e confiabilidade. Investir em calibração e aferição não apenas melhora a qualidade dos produtos e serviços, mas também contribui para a eficiência operacional e a conformidade com normas regulatórias. Portanto, é fundamental que as organizações adotem práticas rigorosas de calibração e aferição, assegurando que seus processos estejam sempre alinhados com os mais altos padrões de qualidade.</p>