Calibração de Transmissor de Pressão: Como Garantir Precisão e Confiabilidade em Seus Processos
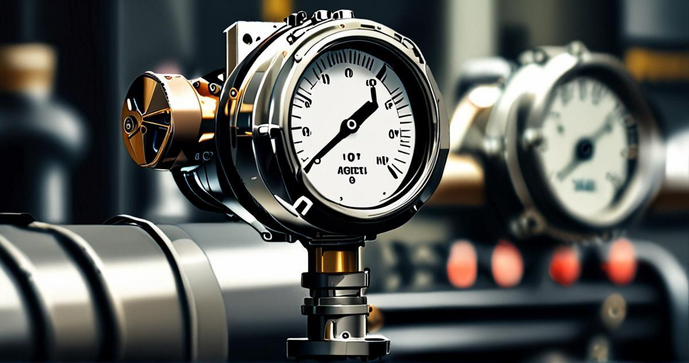
Por: Rafael - 28 de Abril de 2025
<p>A calibração de transmissor de pressão é um processo fundamental para garantir a precisão e a confiabilidade em sistemas de medição industrial. Com a crescente demanda por eficiência e segurança nas operações, a correta calibração desses dispositivos se torna essencial. Neste artigo, abordaremos a importância da calibração, os passos necessários para realizá-la, os erros comuns a serem evitados e a manutenção adequada para prolongar a vida útil dos transmissores de pressão.</p><h2>Importância da Calibração de Transmissores de Pressão na Indústria</h2><p>A calibração de transmissores de pressão é um aspecto crítico na operação de sistemas industriais, pois garante que as medições de pressão sejam precisas e confiáveis. Esses dispositivos são amplamente utilizados em diversas aplicações, como na indústria petroquímica, farmacêutica, alimentícia e de energia, onde a precisão das medições pode impactar diretamente a segurança, a eficiência e a qualidade dos produtos finais.</p><p>Um dos principais motivos para a calibração regular dos transmissores de pressão é a necessidade de manter a precisão das medições. Com o tempo, os sensores podem sofrer desgastes, interferências ambientais ou mudanças nas condições de operação, o que pode levar a desvios nas leituras. Esses desvios podem resultar em decisões erradas, que podem comprometer a segurança dos processos e a qualidade dos produtos. Portanto, a calibração é essencial para garantir que os transmissores operem dentro das especificações estabelecidas pelo fabricante.</p><p>Além disso, a calibração adequada dos transmissores de pressão é fundamental para a conformidade com normas e regulamentos industriais. Muitas indústrias são obrigadas a seguir padrões rigorosos de qualidade e segurança, que incluem a manutenção de equipamentos de medição. A calibração regular não apenas ajuda a atender a esses requisitos, mas também pode evitar penalidades e garantir a continuidade das operações. A falta de conformidade pode resultar em multas, interrupções na produção e até mesmo em ações legais.</p><p>Outro aspecto importante da calibração é a otimização dos processos industriais. Transmissores de pressão calibrados corretamente permitem que os operadores monitorem e ajustem os processos com maior precisão. Isso pode levar a uma melhor eficiência energética, redução de desperdícios e aumento da produtividade. Por exemplo, em uma planta de processamento químico, a pressão inadequada pode resultar em reações ineficientes, afetando a qualidade do produto e aumentando os custos operacionais. Com a calibração adequada, os operadores podem garantir que os processos estejam sempre dentro dos parâmetros ideais.</p><p>A calibração também desempenha um papel crucial na segurança operacional. Em muitas indústrias, a pressão é um parâmetro crítico que deve ser monitorado continuamente. Transmissores de pressão imprecisos podem levar a situações perigosas, como explosões, vazamentos ou falhas de equipamentos. Por exemplo, em uma refinaria de petróleo, uma leitura incorreta da pressão pode resultar em uma explosão catastrófica. Portanto, a calibração regular é uma medida preventiva essencial para garantir a segurança dos trabalhadores e das instalações.</p><p>Além disso, a calibração de transmissores de pressão contribui para a confiabilidade dos dados coletados. Em um ambiente industrial, as decisões são frequentemente baseadas em dados de medição. Se esses dados não forem precisos, as decisões tomadas podem ser prejudiciais. A calibração garante que os dados coletados sejam confiáveis, permitindo que os gerentes e engenheiros tomem decisões informadas sobre operações, manutenção e melhorias de processos.</p><p>Outro ponto a ser considerado é a relação entre a calibração de transmissores de pressão e a utilização de outros equipamentos de medição, como o <a href="https://www.flowmetercalibra.com.br/medidor-vazao-agua-ultrassonico" data-inner-link="Medidor de vazão ultrassônico">Medidor de vazão ultrassônico</a>. A precisão na medição de pressão é muitas vezes interdependente de outras medições, como a vazão. Portanto, a calibração de todos os dispositivos de medição em um sistema deve ser realizada de forma integrada para garantir a precisão geral do processo. A sinergia entre diferentes medições pode resultar em um controle mais eficaz e em uma operação mais segura.</p><p>Por fim, a calibração de transmissores de pressão não deve ser vista apenas como uma tarefa de manutenção, mas como um investimento estratégico. Embora possa haver custos associados à calibração, os benefícios superam amplamente esses custos. A precisão nas medições, a conformidade com normas, a otimização de processos e a segurança operacional são fatores que contribuem para a rentabilidade e a sustentabilidade das operações industriais. Portanto, as empresas devem priorizar a calibração regular de seus transmissores de pressão como parte de sua estratégia de gestão de ativos e melhoria contínua.</p><p>Em resumo, a calibração de transmissores de pressão é vital para garantir a precisão, a segurança e a eficiência nas operações industriais. Com a calibração adequada, as empresas podem não apenas atender aos requisitos regulatórios, mas também otimizar seus processos e garantir a qualidade de seus produtos. A implementação de um programa de calibração robusto é uma prática recomendada que pode trazer benefícios significativos a longo prazo.</p><h2>Passo a Passo para Realizar a Calibração de Transmissores</h2><p>A calibração de transmissores de pressão é um processo essencial para garantir a precisão e a confiabilidade das medições em sistemas industriais. Realizar a calibração de forma adequada envolve uma série de etapas que devem ser seguidas cuidadosamente. Abaixo, apresentamos um guia passo a passo para realizar a calibração de transmissores de pressão.</p><p><strong>1. Preparação e Planejamento</strong></p><p>Antes de iniciar o processo de calibração, é fundamental realizar um planejamento adequado. Isso inclui a definição do equipamento a ser calibrado, a seleção do método de calibração e a preparação do ambiente de trabalho. Certifique-se de que todas as ferramentas e equipamentos necessários estejam disponíveis, como manômetros de referência, fontes de pressão, cabos de conexão e dispositivos de medição. Além disso, é importante revisar o manual do fabricante do transmissor para entender as especificações e os procedimentos recomendados.</p><p><strong>2. Verificação do Equipamento</strong></p><p>Antes de iniciar a calibração, verifique se o transmissor de pressão está em boas condições de funcionamento. Inspecione visualmente o equipamento em busca de danos, corrosão ou vazamentos. Certifique-se de que todas as conexões elétricas e de pressão estejam firmes e seguras. Caso identifique algum problema, é recomendável realizar os reparos necessários antes de prosseguir com a calibração.</p><p><strong>3. Conexão do Equipamento</strong></p><p>Conecte o transmissor de pressão ao equipamento de calibração, como um manômetro de referência. A conexão deve ser feita de acordo com as instruções do fabricante, garantindo que não haja vazamentos. É importante que o manômetro de referência utilizado seja calibrado e tenha uma precisão superior à do transmissor que está sendo calibrado. Isso garantirá que as medições sejam confiáveis e precisas.</p><p><strong>4. Aplicação de Pressão</strong></p><p>Uma vez que o transmissor esteja conectado, comece a aplicar pressão ao sistema. Isso pode ser feito utilizando uma fonte de pressão calibrada, como uma bomba de pressão ou um gerador de pressão. Aplique uma série de pressões conhecidas, variando de zero até o ponto máximo de operação do transmissor. Durante este processo, registre as leituras do transmissor e do manômetro de referência para comparação.</p><p><strong>5. Registro das Leituras</strong></p><p>Enquanto aplica as pressões, é crucial registrar as leituras do transmissor em relação às pressões conhecidas. Crie uma tabela para facilitar a comparação entre as medições do transmissor e as do manômetro de referência. Isso permitirá identificar desvios e determinar a precisão do transmissor em diferentes pontos de operação. A tabela deve incluir pelo menos cinco pontos de calibração, abrangendo toda a faixa de operação do transmissor.</p><p><strong>6. Análise dos Resultados</strong></p><p>Após coletar todas as leituras, analise os resultados para identificar quaisquer desvios entre as medições do transmissor e as do manômetro de referência. Se as leituras estiverem dentro das tolerâncias especificadas pelo fabricante, a calibração pode ser considerada bem-sucedida. No entanto, se houver desvios significativos, será necessário ajustar o transmissor para corrigir as medições.</p><p><strong>7. Ajuste do Transmissor</strong></p><p>Se os resultados da calibração indicarem que o transmissor não está dentro das especificações, será necessário realizar ajustes. A maioria dos transmissores possui um recurso de ajuste que permite calibrar o dispositivo. Siga as instruções do fabricante para realizar os ajustes necessários. Após realizar os ajustes, repita o processo de calibração para garantir que o transmissor agora esteja medindo corretamente.</p><p><strong>8. Documentação</strong></p><p>Uma vez que a calibração tenha sido concluída com sucesso, é importante documentar todo o processo. Registre as leituras, os ajustes realizados e as condições em que a calibração foi realizada. Essa documentação é essencial para garantir a rastreabilidade e a conformidade com normas e regulamentos. Além disso, manter um histórico de calibrações pode ajudar a identificar padrões de desempenho e a programar futuras calibrações.</p><p><strong>9. Manutenção Regular</strong></p><p>A calibração não deve ser vista como uma tarefa única, mas sim como parte de um programa de manutenção regular. É recomendável estabelecer um cronograma de calibração com base nas recomendações do fabricante e nas condições de operação do transmissor. A calibração regular ajudará a garantir que o transmissor continue a operar com precisão ao longo do tempo.</p><p>Se você não se sentir confortável realizando a calibração por conta própria, considere contratar <a href="https://www.flowmetercalibra.com.br/empresas-calibracao-equipamentos" data-inner-link="Empresas de calibração de equipamentos">empresas de calibração de equipamentos</a> especializadas. Esses profissionais possuem o conhecimento e as ferramentas necessárias para garantir que a calibração seja realizada de forma adequada e eficiente.</p><p>Em resumo, a calibração de transmissores de pressão é um processo crítico que envolve várias etapas, desde a preparação até a documentação dos resultados. Seguir este passo a passo garantirá que os transmissores operem com precisão e confiabilidade, contribuindo para a segurança e a eficiência das operações industriais.</p><h2>Erros Comuns na Calibração e Como Evitá-los</h2><p>A calibração de transmissores de pressão é um processo crítico que garante a precisão e a confiabilidade das medições em sistemas industriais. No entanto, existem diversos erros que podem ocorrer durante esse processo, comprometendo a eficácia da calibração e, consequentemente, a operação do sistema. Neste artigo, abordaremos os erros mais comuns na calibração de transmissores de pressão e como evitá-los.</p><p><strong>1. Falta de Planejamento Adequado</strong></p><p>Um dos erros mais frequentes na calibração é a falta de um planejamento adequado. Muitas vezes, os profissionais iniciam o processo sem uma estratégia clara, o que pode levar a medições imprecisas e a um uso ineficiente do tempo. Para evitar esse erro, é fundamental elaborar um plano detalhado que inclua a definição dos equipamentos a serem calibrados, a seleção dos métodos de calibração e a preparação do ambiente de trabalho. Além disso, é importante garantir que todas as ferramentas e equipamentos necessários estejam disponíveis antes de iniciar o processo.</p><p><strong>2. Uso de Equipamentos Não Calibrados</strong></p><p>Outro erro comum é utilizar equipamentos de medição que não estão calibrados. Por exemplo, se um manômetro de referência não estiver calibrado, as medições realizadas durante a calibração do transmissor de pressão podem ser imprecisas. Para evitar esse problema, sempre verifique a calibração de todos os instrumentos utilizados no processo. Utilize apenas equipamentos que tenham um histórico de calibração recente e que atendam às especificações necessárias para a tarefa.</p><p><strong>3. Ignorar as Condições Ambientais</strong></p><p>As condições ambientais podem ter um impacto significativo nas medições de pressão. Fatores como temperatura, umidade e vibração podem afetar o desempenho dos transmissores e dos equipamentos de calibração. Ignorar essas condições pode resultar em medições imprecisas. Para evitar esse erro, é importante realizar a calibração em um ambiente controlado, onde as condições possam ser monitoradas e mantidas dentro dos limites especificados pelo fabricante. Se a calibração for realizada em um ambiente industrial, considere as variações que podem ocorrer e ajuste os procedimentos conforme necessário.</p><p><strong>4. Não Realizar Múltiplas Leituras</strong></p><p>Um erro comum durante a calibração é não realizar múltiplas leituras em cada ponto de calibração. Confiar em uma única leitura pode levar a conclusões erradas sobre a precisão do transmissor. Para evitar esse problema, sempre faça várias medições em cada ponto de calibração e calcule a média das leituras. Isso ajudará a identificar quaisquer desvios e a garantir que as medições sejam consistentes.</p><p><strong>5. Falta de Documentação</strong></p><p>A documentação é uma parte essencial do processo de calibração, mas muitas vezes é negligenciada. A falta de registros adequados pode dificultar a rastreabilidade e a conformidade com normas e regulamentos. Para evitar esse erro, mantenha um registro detalhado de todas as calibrações realizadas, incluindo as leituras, os ajustes feitos e as condições em que a calibração foi realizada. Essa documentação é fundamental para garantir a conformidade e para futuras referências.</p><p><strong>6. Não Ajustar o Transmissor Após a Calibração</strong></p><p>Após a calibração, é comum que os profissionais se esqueçam de ajustar o transmissor, caso as medições não estejam dentro das especificações. Ignorar essa etapa pode resultar em medições imprecisas e em problemas operacionais. Para evitar esse erro, sempre verifique se o transmissor precisa de ajustes após a calibração e siga as instruções do fabricante para realizar as correções necessárias.</p><p><strong>7. Subestimar a Importância da Manutenção Regular</strong></p><p>A calibração não deve ser vista como uma tarefa única, mas sim como parte de um programa de manutenção regular. Subestimar a importância da manutenção pode levar a falhas no desempenho do transmissor ao longo do tempo. Para evitar esse erro, estabeleça um cronograma de calibração e manutenção com base nas recomendações do fabricante e nas condições de operação do transmissor. A manutenção regular ajudará a garantir que o transmissor continue a operar com precisão e confiabilidade.</p><p><strong>8. Ignorar a Interdependência com Outros Equipamentos</strong></p><p>Os transmissores de pressão muitas vezes trabalham em conjunto com outros dispositivos de medição, como o <a href="https://www.flowmetercalibra.com.br/venda-medidores-vazao" data-inner-link="Medidor de vazão">medidor de vazão</a>. Ignorar a interdependência entre esses equipamentos pode resultar em medições imprecisas e em problemas operacionais. Para evitar esse erro, sempre considere a relação entre os diferentes dispositivos de medição e realize a calibração de forma integrada. Isso garantirá que todos os equipamentos estejam funcionando corretamente e que as medições sejam precisas.</p><p><strong>9. Não Treinar Adequadamente a Equipe</strong></p><p>A falta de treinamento adequado da equipe responsável pela calibração pode levar a erros significativos. Profissionais não treinados podem não seguir os procedimentos corretos, resultando em medições imprecisas. Para evitar esse erro, invista em treinamento contínuo para a equipe, garantindo que todos estejam atualizados sobre as melhores práticas e os procedimentos de calibração. Isso não apenas melhorará a precisão das medições, mas também aumentará a segurança operacional.</p><p>Em resumo, a calibração de transmissores de pressão é um processo complexo que pode ser afetado por diversos erros. Ao estar ciente desses erros comuns e implementar medidas para evitá-los, as empresas podem garantir que seus sistemas de medição operem com precisão e confiabilidade. A calibração adequada não apenas melhora a eficiência operacional, mas também contribui para a segurança e a qualidade dos produtos finais.</p><h2>Manutenção e Verificação Regular de Transmissores de Pressão</h2><p>A manutenção e verificação regular de transmissores de pressão são essenciais para garantir a precisão e a confiabilidade das medições em sistemas industriais. Esses dispositivos desempenham um papel crucial em diversas aplicações, desde o monitoramento de processos até a segurança operacional. Neste artigo, discutiremos a importância da manutenção regular, as melhores práticas e os benefícios de manter os transmissores de pressão em condições ideais.</p><p><strong>1. Importância da Manutenção Regular</strong></p><p>A manutenção regular dos transmissores de pressão é fundamental para evitar falhas e garantir que os dispositivos operem dentro das especificações. Com o tempo, fatores como desgaste, corrosão e variações ambientais podem afetar o desempenho dos transmissores. A falta de manutenção pode resultar em medições imprecisas, comprometendo a segurança e a eficiência dos processos industriais. Portanto, estabelecer um cronograma de manutenção é uma prática recomendada que pode prevenir problemas futuros e prolongar a vida útil dos equipamentos.</p><p><strong>2. Frequência da Manutenção</strong></p><p>A frequência da manutenção dos transmissores de pressão pode variar dependendo de vários fatores, incluindo o tipo de aplicação, as condições ambientais e as recomendações do fabricante. Em geral, é aconselhável realizar verificações regulares a cada seis meses ou anualmente. No entanto, em ambientes industriais mais exigentes, pode ser necessário aumentar a frequência das manutenções. É importante monitorar o desempenho dos transmissores e ajustar o cronograma de manutenção conforme necessário.</p><p><strong>3. Inspeção Visual</strong></p><p>Uma das etapas mais simples, mas eficazes, na manutenção de transmissores de pressão é a inspeção visual. Durante essa inspeção, verifique se há sinais de danos, corrosão ou vazamentos. Inspecione as conexões elétricas e de pressão para garantir que estejam firmes e seguras. Qualquer anomalia identificada deve ser tratada imediatamente para evitar problemas maiores no futuro. A inspeção visual deve ser realizada regularmente, mesmo entre as manutenções programadas.</p><p><strong>4. Calibração Regular</strong></p><p>A calibração é uma parte essencial da manutenção de transmissores de pressão. Mesmo que os dispositivos estejam funcionando corretamente, é importante realizar calibrações regulares para garantir que as medições permaneçam precisas. A calibração deve ser realizada de acordo com as recomendações do fabricante e sempre que houver alterações nas condições de operação. Se você não se sentir confortável realizando a calibração, considere contratar uma <a href="https://www.flowmetercalibra.com.br/empresas-calibracao-instrumentos-medicao-sp" data-inner-link="Empresa de calibração de instrumentos de medição">empresa de calibração de instrumentos de medição</a> especializada para garantir que o processo seja realizado corretamente.</p><p><strong>5. Limpeza dos Transmissores</strong></p><p>A limpeza dos transmissores de pressão é uma parte importante da manutenção. A sujeira e os contaminantes podem se acumular nos dispositivos, afetando seu desempenho. Utilize um pano limpo e seco para remover a poeira e a sujeira acumulada. Evite o uso de produtos químicos agressivos que possam danificar os componentes. A limpeza deve ser realizada regularmente, especialmente em ambientes industriais onde a sujeira pode ser um problema constante.</p><p><strong>6. Verificação dos Sensores</strong></p><p>Os sensores dos transmissores de pressão são componentes críticos que devem ser verificados regularmente. Certifique-se de que os sensores estejam limpos e livres de obstruções. Qualquer sujeira ou detrito que bloqueie o sensor pode resultar em medições imprecisas. Além disso, verifique se os sensores estão calibrados corretamente e funcionando dentro das especificações. Se houver dúvidas sobre o desempenho dos sensores, é recomendável realizar testes adicionais ou substituí-los, se necessário.</p><p><strong>7. Monitoramento de Desempenho</strong></p><p>O monitoramento contínuo do desempenho dos transmissores de pressão é uma prática recomendada que pode ajudar a identificar problemas antes que se tornem críticos. Utilize sistemas de monitoramento que permitam acompanhar as medições em tempo real e detectar desvios. Se as medições começarem a apresentar inconsistências, isso pode ser um sinal de que a manutenção é necessária. O monitoramento proativo pode ajudar a evitar falhas inesperadas e garantir a continuidade das operações.</p><p><strong>8. Treinamento da Equipe</strong></p><p>Uma equipe bem treinada é fundamental para garantir a manutenção eficaz dos transmissores de pressão. Invista em treinamento contínuo para os profissionais responsáveis pela manutenção e calibração dos dispositivos. O conhecimento adequado sobre os procedimentos corretos e as melhores práticas pode fazer uma grande diferença na eficácia da manutenção. Além disso, a equipe deve estar ciente da importância da manutenção regular e das consequências de negligenciá-la.</p><p><strong>9. Documentação e Registro</strong></p><p>Manter registros detalhados de todas as atividades de manutenção e calibração é essencial para garantir a rastreabilidade e a conformidade com normas e regulamentos. Documente todas as inspeções, calibrações, ajustes e reparos realizados nos transmissores de pressão. Essa documentação pode ser útil para auditorias e para identificar padrões de desempenho ao longo do tempo. Além disso, manter um histórico de manutenção pode ajudar a programar futuras atividades e a identificar a necessidade de substituições.</p><p><strong>10. Benefícios da Manutenção Regular</strong></p><p>A manutenção e verificação regular de transmissores de pressão trazem uma série de benefícios. Além de garantir a precisão das medições, a manutenção regular ajuda a prolongar a vida útil dos equipamentos, reduzindo a necessidade de substituições frequentes. Isso resulta em economia de custos a longo prazo e em uma operação mais eficiente. Além disso, a manutenção adequada contribui para a segurança operacional, minimizando o risco de falhas que podem levar a acidentes ou interrupções na produção.</p><p>Em resumo, a manutenção e verificação regular de transmissores de pressão são essenciais para garantir a precisão, a confiabilidade e a segurança das medições em sistemas industriais. Ao seguir as melhores práticas de manutenção, as empresas podem evitar problemas operacionais, prolongar a vida útil dos equipamentos e garantir a eficiência de seus processos. Investir em manutenção regular é uma estratégia inteligente que traz benefícios significativos a longo prazo.</p><p>Em conclusão, a calibração de transmissores de pressão é uma prática indispensável para assegurar a precisão e a confiabilidade das medições em ambientes industriais. Através de um processo bem estruturado, que inclui planejamento, verificação regular e manutenção adequada, é possível evitar erros comuns que podem comprometer a segurança e a eficiência operacional. Investir na calibração e na manutenção desses dispositivos não apenas prolonga sua vida útil, mas também contribui para a otimização dos processos e a conformidade com normas regulatórias. Portanto, é essencial que as empresas adotem uma abordagem proativa em relação à calibração, garantindo assim a integridade e a eficácia de suas operações.</p>